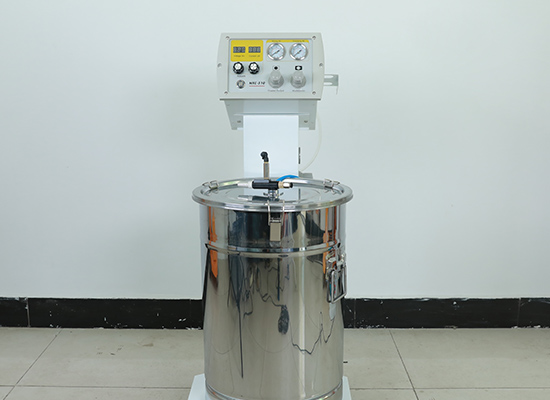
Before starting the operation of
Professional Powder Coating Equipment, always conduct a thorough inspection. Check the powder feeder for any signs of powder clumping or blockages. Use a brush or compressed air to clean it if necessary. Inspect the spray gun nozzles to ensure they are clean and free from any debris. A clogged nozzle can lead to uneven coating. Also, verify that the electrostatic generator is functioning properly by checking the voltage and current readings.
When setting up the equipment, pay close attention to the grounding. A proper ground connection is crucial for the electrostatic charging process. It ensures that the charged powder particles are attracted evenly to the object. If the grounding is faulty, you may experience inconsistent powder adhesion.
During the coating process, start with a test object. This allows you to adjust the powder flow rate, air pressure, and spray pattern without wasting a large amount of powder or ruining the actual product. For example, if you're coating a new type of object, begin with a small, similar - shaped test piece. Adjust the powder flow rate gradually until you achieve a smooth and even coating. A lower powder flow rate is often better for detailed work, while a higher rate can be used for covering large areas quickly.
The spray gun's movement is another important aspect. Move the spray gun in a smooth, continuous motion. Avoid sudden stops or starts, as this can cause uneven coating thickness. Overlap each pass of the spray gun slightly to ensure complete coverage. The distance between the spray gun and the object should be kept consistent. As a general rule, a distance of 15 - 30 cm is recommended, but this may vary depending on the type of spray gun and the object's surface.
Maintenance of
Professional Powder Coating Equipment is key to its long - term performance. After each use, clean the spray gun thoroughly. Use a suitable cleaning solution to remove any powder residue from the nozzle, air cap, and the gun's interior. This not only prevents clogs but also extends the life of the gun. The powder feeder should also be emptied and cleaned to prevent powder caking. Regularly check the filters in the powder recovery system. Clogged filters can affect the powder flow and the overall performance of the equipment.
The curing oven in the
Professional Powder Coating Equipment requires special attention. Calibrate the temperature sensors regularly to ensure accurate temperature control. Use a reliable thermometer to verify the oven's temperature. An incorrect temperature can lead to under - cured or over - cured coatings. Under - cured coatings may lack durability, while over - cured coatings can become brittle.
In case of common problems, such as powder not adhering well, first check the surface preparation of the object. Ensure that it is clean, degreased, and properly primed. If the problem persists, check the electrostatic charging system. A malfunctioning electrostatic generator can cause poor powder adhesion. For uneven coating, check the spray gun settings, including air pressure, powder flow rate, and spray pattern. Adjust these settings as needed.
Disclaimer: Enhance your coating process with advanced electrostatic powder coating machines, precision powder coating spray guns, comprehensive powder coating systems, and efficient powder coating lines from Hangzhou Huaxiang Coating Equipment Co., Ltd. Designed for reliability and high-quality finishes, our solutions meet all your industrial powder coating machine needs. Contact us at sale3@cncolourspray.com